Advanced Techniques in Metal Stamping for Precision Production
As sectors constantly demand better resistances and intricate styles in their steel components, the pursuit for advanced techniques in metal marking has actually increased. From the usage of advanced multi-stage stamping procedures to the integration of sophisticated automation technologies, the landscape of metal stamping is undergoing an extensive change.
Advanced Multi-Stage Stamping Processes
Discussing the intricacies of sophisticated multi-stage marking procedures exposes the innovative methods used in contemporary production practices. Metal Stamping. Multi-stage marking is a complicated procedure that involves several actions to change a level sheet of metal right into a last stamped item. Making use of progressive passes away, where different procedures are carried out at each stage of the stamping process, enables for high precision and effectiveness in the production of intricate steel components
Throughout the preliminary stages of multi-stage stamping, the level metal sheet is fed right into the marking press, where a collection of dies are made use of to reduce and form the material. Succeeding phases involve extra creating, flexing, and punching procedures to further fine-tune the part. Each phase is very carefully developed to develop upon the previous one, leading to the development of complicated geometries with limited tolerances.
Advanced multi-stage marking procedures need a high degree of expertise and precision to guarantee the top quality and consistency of the stamped components. By utilizing sophisticated machinery and tooling, makers can produce a vast array of metal elements with performance and accuracy.
Precision Tooling Innovations
Accuracy tooling technologies have actually transformed the metal stamping industry, improving performance and high quality in producing processes. These advancements have considerably affected the means steel components are generated, leading to higher precision and uniformity in the end products. One key advancement is the development of computer system numerical control (CNC) technology in tooling style and manufacture. CNC systems permit elaborate designs to be converted directly right into tooling, guaranteeing precision and repeatability in the marking process.
Additionally, the integration of sensors and real-time monitoring capabilities in precision tooling has made it possible for suppliers to discover and resolve concerns promptly, decreasing downtime and minimizing scrap prices. By integrating smart modern technology right into tooling, operators can maximize parameters such as pressure, speed, and alignment during the marking procedure, leading to boosted product top quality and raised efficiency.
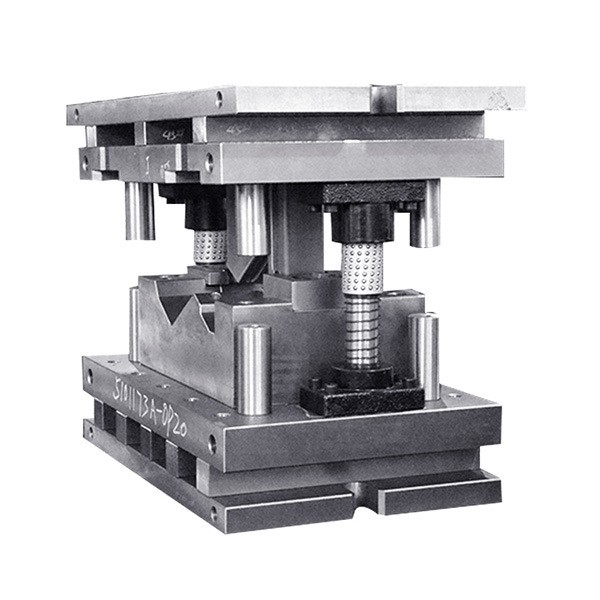
Automation in Metal Stamping
The development of accuracy tooling developments in the metal stamping market has actually led the way for considerable innovations in automation, transforming the manufacturing landscape towards boosted efficiency and efficiency. Metal Stamping. Automation in metal stamping involves making use of advanced machinery and robotics to execute different jobs typically performed by human drivers. This shift towards automation supplies many benefits, consisting of improved accuracy, much faster manufacturing cycles, and decreased labor prices
One trick facet of automation in steel marking is the execution of computer numerical control (CNC) systems, which enable accurate control over the marking process. CNC modern technology permits the development of facility and detailed steel get rid of regular quality. Additionally, automated systems can be set to run continuously, resulting in higher outcome prices and much shorter lead times.
Furthermore, automation enhances workplace safety by reducing manual handling of heavy materials and decreasing the threat of mishaps (Metal Stamping). As manufacturing sectors continue to embrace automation, the future of steel stamping holds great promise for also greater performance and innovation
High-Speed Stamping Methods

Among the main advantages of high-speed stamping strategies is the capability to create a large volume of parts in a much shorter quantity of time contrasted to traditional stamping methods. This increased productivity not only permits producers to meet limited production target dates yet additionally allows price financial savings with economic situations of range. Furthermore, high-speed marking can assist lower product waste by optimizing the material use during the marking procedure.
Furthermore, high-speed stamping methods usually incorporate ingenious features such as quick die adjustment systems and real-time surveillance capabilities, better improving the total effectiveness and versatility of the steel stamping procedure. As innovation continues to breakthrough, high-speed marking is anticipated to play an important function in driving the future of accuracy production.
Top Quality Control in Stamping Procedures
Efficient quality assurance procedures are necessary for ensuring the dependability and uniformity of steel stamping procedures. Quality assurance in stamping procedures involves a series of organized processes focused on spotting and pop over to these guys stopping defects in the made elements. One essential facet of quality assurance in metal marking is the use of advanced examination strategies such as blog optical examination systems and coordinate determining devices (CMMs) to validate the measurements and resistances of stamped parts.
In addition, quality control measures in marking operations usually include the application of analytical procedure control (copyright) techniques to keep an eye on the production process in real-time and guarantee that it remains within appropriate limits. By examining information and identifying fads, manufacturers can proactively attend to any type of deviations from the desired high quality standards.
Moreover, top quality control in steel stamping operations likewise involves thorough material screening to make certain that the raw materials made use of meet the needed specifications for the marking process. This may include carrying out product hardness tests, tensile stamina examinations, and dimensional inspections to assure the quality and integrity of the stamped parts. Generally, executing durable quality assurance actions is essential for achieving top notch stamped parts consistently.
Verdict
To conclude, advanced methods in steel marking play a crucial function in precision production procedures. With multi-stage stamping procedures, ingenious tooling options, automation, high-speed methods, and rigorous quality control actions, suppliers can attain higher degrees of accuracy and effectiveness in their operations. These advancements in metal marking technology have actually allowed firms to create complex components with tight resistances, inevitably leading to read more enhanced item high quality and client fulfillment in the manufacturing industry.